Vliegtuigen, boten, machines en grote motoren die uit gebruik worden genomen, bevatten heel wat hoogwaardige materialen en onderdelen die opnieuw kunnen worden hergebruikt. Koen Staut, CEO van de Belgische scale-up Aerocircular, legt uit hoe hij hier op maar liefst drie continenten een succesvol businessmodel rond opzet.
Tekst: Joris Hendrickx – foto’s: Kris Van Exel
Wat maakt jullie aanpak zo uniek?
“We zien een vliegtuig dat aan het einde van zijn economische levensduur is als een doos met materialen. Op zich is het idee van vliegtuigontmanteling niet nieuw, maar we zijn er wel als eerste in geslaagd om er een ecologisch verhaal van te maken, dat ook nog eens economisch rendabel is. We zijn voor onze financiering niet afhankelijk van subsidies. Dit is mogelijk door steeds te zoeken naar meerwaarde, waardoor onze klanten bereid zijn om ons als dienstverlener te betalen. We creëren zelfs zodanig veel meerwaarde voor onze klanten dat we met hen hebben kunnen afspreken dat de helft van de meerwaarde bij ons mag blijven om onze R&D-afdeling verder uit te bouwen.”
“Momenteel hebben we al een operationele site in Oostende. Deze zomer komt daar een ontmantelingslocatie bij in Phoenix (Arizona) en in 2021 nog een in Abu Dhabi. Het doel van deze werkplaatsen is om vliegtuigen zo veel mogelijk – volgens ons ontmantelingsplan – te ontdoen van onderdelen en componenten om vervolgens in het kader van de circulaire gedachte maximaal aan kwalitatieve herbestemming te doen.”
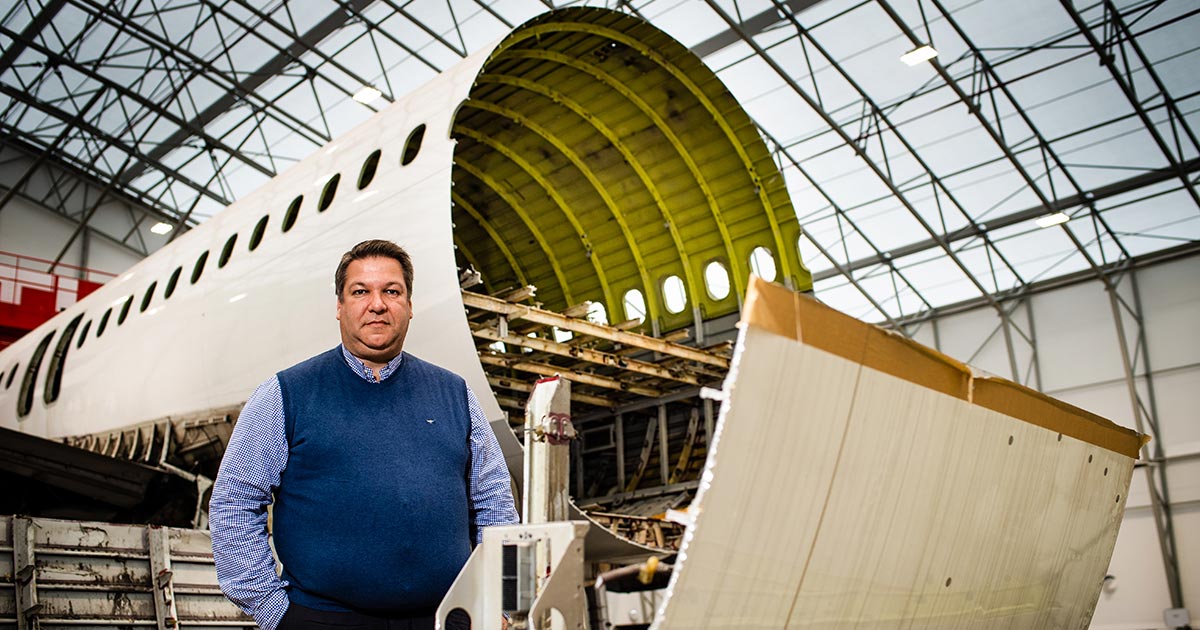
Hoe gaan jullie precies tewerk?
“Voor ieder onderdeel van een vliegtuig hebben we drie mogelijke stromen. De eerste stroom is het hergebruik van onderdelen in de luchtvaart. Klanten die hun vliegtuig door ons laten ontmantelen, geven ons een lijst van gemiddeld 250 à 300 onderdelen die ze zelf graag terug willen. In totaal bevat een operationeel vliegtuig echter ongeveer 450 componenten die interessant kunnen zijn als wisselstuk. Dat betekent dat we 150 à 200 componenten vermarkten via onze partners die deze vervolgens terug aanbieden aan onderhoudsbedrijven. Deze eerste stroom is een relatief stabiele stroom van herbestemming en leunt het dichtst aan bij de circulaire economie.”
“In de tweede stroom gebruiken we materialen en onderdelen zoals ze oorspronkelijk ontworpen zijn, maar met een andere bestemming. Zo wordt bijvoorbeeld met een gigantische zaag de volledige cockpit van het vliegtuig losgezaagd, zodat deze kan worden geconverteerd tot vliegsimulator door een Belgisch bedrijf dat daarin is gespecialiseerd. Zo’n volledige herbestemming is uiteraard beter dan het downgraden van de verschillende materialen. Bovendien is de manipulatiekost relatief laag, waardoor er een hoog rendement is. Maar we kunnen de romp ook in secties zagen die vervolgens kunnen dienen als pop-up bars, sleeprooms op festivals,…”
De expertise, het netwerk en het ecosysteem dat we hebben opgebouwd, kunnen we ook aanbieden aan andere sectoren, zoals de scheepvaart, machinebouw en zelfs motoren van boorplatformen.
“In de derde stroom gebruiken we materialen opnieuw als grondstof. Voor ieder onderdeel zijn er duurzame herbestemmingen op materiaalgebied. Het mooiste voorbeeld is dat we het aluminium van de buitenzijde van de romp in een specifieke combinatie smelten met de binnenstructuur en de klinknagels, waardoor een nieuwe legering ontstaat die perfect voldoet aan de karakteristieken om poeder voor 3D-printers te maken. Zo genereren we een meerwaarde van een brutofactor honderd op de schrootwaarde. In een volgende stap zullen we dat poeder laten certifiëren om opnieuw luchtvaartonderdelen van te printen, zodat de cirkel volledig rond is. Het is uiteraard onze dagelijkse oefening om de beste bestemming van deze drie telkens opnieuw te kiezen en te evalueren.”
Jullie hebben jullie activiteiten ook uitgebreid buiten de luchtvaart. Waarom?
“Het laatste halfjaar kregen we zeer veel vragen van buiten de luchtvaart. Daarom hebben we besloten om onze R&D-afdeling los te koppelen en als aparte entiteit te laten verdergaan onder de naam ‘Industrial Circularity Lab’. De expertise, het netwerk en het ecosysteem dat onze mensen binnen die afdeling hebben opgebouwd, kunnen we zo ook aanbieden aan andere sectoren, zoals de scheepvaart, machinebouw en zelfs motoren van boorplatformen. Ook daar is er immers heel wat potentieel om te herbestemmen waar onze expertise een meerwaarde kan opleveren. We worden intussen door heel wat grote spelers erkend: we maken samen met grote namen uit de luchtvaart- en academische wereld deel uit van diverse Europese subsidietrajecten.”
We slagen er als eerste bedrijf in om het circulaire gedachtegoed te valoriseren in een rendabel project.
“Daarnaast ontwikkelen we tools. Zo hebben we een machine ontwikkeld en gepatenteerd, waarmee je klinknagels zeer efficiënt uit de romp van een vliegtuig kan verwijderen. Met deze kop kan dat aan tien klinknagels per seconde, terwijl het met andere tools tien seconden per klinknagel duurt. Het interessante hieraan is dat deze tool ook heel nuttig is voor bijvoorbeeld repairshops. Er is dus zeker een enorme markt voor.”
Hoe belangrijk zijn jullie partners in dit verhaal?
“Voor de derde stroom, waarbij we materialen herbestemmen tot grondstof, gaan we nooit zelf de markt op. We zoeken steeds een gerenommeerde partij die geïnteresseerd is om samen met ons de markt te betreden of die deze materialen zelf in zijn productie kan gebruiken. Zo kunnen we blijven concentreren op de productontwikkeling, en kunnen we de expertise van anderen benutten om marketing, sales en distributie op te zetten. Het geeft zekerheid van de afzet van ons materiaal. Het bijkomende resultaat van zulke samenwerkingen is vaak dat onze R&D-afdelingen beginnen samen te werken en elkaar zo verrijken. Door de garantie van de afzet trekken we ook heel wat gereputeerde onderzoeksinstellingen aan. We doen enorm veel ervaring op en worden ook zeer goed ondersteund door het ecosysteem van leveranciers, klanten en partners dat we intussen hebben uitgebouwd.”
Waarom zijn jullie als start-up meteen opgestart in drie continenten?
“De markt waarin we werken maakte dit voor ons noodzakelijk. Bovendien is het een ideale manier om ons intellectueel eigendom beschermen. Op zich doen we niets nieuws, buiten dan de zaken die we effectief hebben gepatenteerd. We hebben vooral bestaande processen op een andere, nieuwe en vooral circulaire manier aan elkaar geschakeld. Op die manier slagen we er als eerste bedrijf in om het circulaire gedachtegoed te valoriseren in een rendabel project. Het risico snel te worden gekopieerd blijft een bijzonder aandachtspunt, waardoor we deze markten dan ook zo snel mogelijk zelf wilden claimen.”
Grootste portaalzaag ter wereld staat in Oostende
Hilti ontwikkelde voor Aerocircular een enorme portaalzaag om met een chirurgische precisie vliegtuigen in secties te snijden. Hiermee wordt het mogelijk om op een kwalitatieve en efficiënte manier hoogwaardige materialen uit vliegtuigen te recupereren. Meer uitleg door Johan Lauwers, Global Key Project & Specials Manager bij Hilti Corporation in Liechtenstein.

“Onze portaalzaag die in Oostende wordt gebruikt door Aerocircular is de grootste ter wereld. Deze is speciaal gemaakt voor vliegtuigen van het type A320 – B737 (narrow body). We hebben echter ook plannen om een nóg grotere versie te maken die type A380 – B747 (wide body) aankan. Deze zal door Aerocircular worden gebruikt op hun site in het Midden-Oosten.”
Ruime ervaring in uitdagende projecten
“Op zich is dit soort van projecten niet nieuw voor Hilti. Zo zijn we bijvoorbeeld erg actief in de ontmanteling van radioactieve installaties van kerncentrales. We doen dat in speciale werkplaatsen, maar ook op de site zelf. Vaak worden bij kerncentrales immers eerst de enorme installaties gebouwd, en daarna pas het gebouw dat errond staat. Om zo’n installatie buiten te krijgen, moet ze dus eerst ter plekke in stukken worden gezaagd. Bij een kerncentrale vormt het secundaire afval trouwens traditioneel een groot probleem in de ontmanteling. Klassieke ontmantelingsmethodes maken immers gebruik van een koelmedium, dat dan radioactief wordt. Onze technologie laat toe om alles droog te zagen, wat beter past in het circulaire gedachtegoed.”
Veilig en efficiënt
“Het gebruik van een diamantkabel om te zagen, is veiliger én efficiënter. Het grootste voordeel ten opzichte van andere methodes is dat je zeker kan zijn dat werkelijk alles gesneden is. Met diamant kunnen bovendien alle materialen worden gesneden: staal, aluminium, beton, asfalt, plastic, glas,… Tot slot kan dit type zaag volledig vanop afstand worden bestuurd, er is geen enkele interventie meer nodig van de operator aan het stuk zelf.”
Circulair ontwerp
“Ook de zaag zelf is opgebouwd volgens het circulaire principe, mede gestuurd door Aerocircular. Dit is trouwens een van de vele raakpunten die onze partnership zo uitdagend en interessant maakt. Maar liefst 95% van onze machine is volledig recycleerbaar op het einde van de levensduur. Enkel de isolatie van de elektrische kabels en de slijtring op de pulleys bestaan uit kunststof. De rest bestaat uit verschillende recupereerbare metaalsoorten.”
In samenwerking met